化学工业深入我们日常生活的方方面面,也影响着我们的生活质量,是我国的重要支柱产业。化学工业的一个重要特点就是高能耗,但对能量的利用的效率比较低,尤其在我国,能量的利用效率大约是33%,比发达国家约低10%。目前,人们越来越重视节能,国外已经开发并应用了各种节能技术,作为化工的我们有必要了解这些节能技术。目前比较常见的节能技术包括热泵精馏、多效蒸发、多效精馏、侧线出料、热偶精馏(隔壁塔)、夹点技术等。
文章源自云智设计-https://www.cidrg.com/news/training-news/16092.html
1夹点设计概述
化工工艺过程中存在多股需要加热或者冷却的物流,此外还有冷热公用工程,这些物流可以在温-焓( T-H) 图中分别合并成冷热物流符合曲线。当在水平方向上,两曲线相互靠近直到达到最小的传热温差△Tmin时,热回收的量达到最大,公用工程达到最小,两曲线最靠近的地方为夹点,其中温度高的叫热夹点,温度低的叫冷夹点。文章源自云智设计-https://www.cidrg.com/news/training-news/16092.html
换热网络的夹点设计手段是由国外的以Linn Hoff教授为首的研究小组提出的,现在成为换热网络设计的首要采用的方法。通过夹点技术的设计,可以很大程度上减少能量的浪费,这种方法已大量运用于化工的生产,该技术在指导化工节能方面提供了理论基础,对化工的节能具有很大指导的作用。文章源自云智设计-https://www.cidrg.com/news/training-news/16092.html
2夹点位置的确定
确定夹点位置的方法主要有两种:T-H图法和问题表法。文章源自云智设计-https://www.cidrg.com/news/training-news/16092.html
(1)T-H图法文章源自云智设计-https://www.cidrg.com/news/training-news/16092.html
在T-H图上可以直观的描述夹点位置,为确定过程系统的夹点,需要给出下列数据:所有过程物流的流量、组成、压力、初始温度、目标温度、以及选用的冷热物流间匹配换热的最小允许传热温差△Tmin。用作图的方法在T-H图上确定夹点位置的步骤如下:文章源自云智设计-https://www.cidrg.com/news/training-news/16092.html
1) 根据给出的冷、热物流的数据,在T-H图上分别作出热物流组合曲线及冷物流组合曲线。文章源自云智设计-https://www.cidrg.com/news/training-news/16092.html
2) 热组合曲线置于冷组合曲线的上方,并且让两者在水平方向相互靠拢,当两组合曲线在某处的垂直距离刚好等于△Tmin时,该处即为夹点。文章源自云智设计-https://www.cidrg.com/news/training-news/16092.html
(2)问题表法文章源自云智设计-https://www.cidrg.com/news/training-news/16092.html
T-H图法主要针对物流比较少,要求不精确的流程,但当物流比较多并要求精确确定夹点时,T-H图法就明显不如问题表法便捷,但计算步骤比较繁琐。文章源自云智设计-https://www.cidrg.com/news/training-news/16092.html
3夹点技术的基本设计原则
夹点将换热系统分为两部分,为了减少公用工程的消耗量,一个完整的换热网络应该遵循以下三个原则:
(1)不应有跨越夹点的传热;
(2)夹点之上不应设置任何公用工程冷却器;
如果违背这三条原则,则会造成公用工程的浪费,因为如果多消耗一种公用工程,就需要用另一种公用工程加热或者冷却。
4换热网络优化的基本准则
(1)流股数目准则
根据夹点设计的基本原则,夹点之上只能用热公用工程加热,同理夹点之下只能用冷公用工程冷却,如果违背此原则,会造成公用工程的浪费,流股数目准则如下:
1)对于夹点上方,热物流(包括其分支物流)的数目要小于或等于冷物流(包括其分支物流)数目,即:
2)对于夹点上方,热物流(包括其分支物流)的数目要大于或等于冷物流(包括其分支物流)数目,即:
(2)热容流率准则
为保证温差不小于△Tmin,夹点处匹配的流股的热容流率需满足以下准则:
1)对于夹点上方,每一夹点匹配中热物流(或其分支)的热容流率要小于或等于冷物流的热容流率:
2)对于夹点下方,则:
此外,在满足以上两个原则的前提下,为了使换热器的数量达到最少,减少设备投资的费用,每一次换热匹配时应该使其中一条物流达到换热目标。
5.问题表法
我们已经知道换热网络的设计方法分别是T-H图法和问题表法,鉴于T-H图法的设计精度不够精确,此处便以具体事例给出详细的问题表法设计过程。
表5-1 物流参数
物流编号和类型 | 热容流率CP/(Kw/℃) | 进口温度/℃ | 出口温度/℃ |
1 热物流 | 3 | 150 | 40 |
2 热物流 | 1.5 | 170 | 65 |
3 冷物流 | 2.0 | 30 | 120 |
4 冷物流 | 4.0 | 80 | 140 |
表5-1是相关的物流参数,最小的传热温差我们取10℃,试设计该换热系统的换热网络及夹点位置和公用工程的用量。
5.1 温区的划分
1.将所有的冷热物流的温度分别从小到大排列。
热物流:40 65 150 170
冷物流:30 80 120 140
2.计算冷热物流的平均温度,即热物流温度下降最小温差的一半(5℃),冷物流上升最小温差的一半(5℃)。
热物流:35 60 145 165
冷物流:35 85 125 145
3.将所有的冷热物流的平均温度从小到大排列。
35 60 85 125 145 165
4.温区划分。
分区划分如图1.
图1 温区划分
5.2温区内热平衡计算
热平衡的计算式如下:
式中:
△H ——第i温区所需的外加热量,kw;
——该温区内冷热物流热容流率之和,(Kw/℃);
Ti, Ti+1——该温区内进出口温度,℃;
由以上计算式可以求得每个温区的所需的外加热量。
第一温区:=-1.5(165-145)=-30Kw
第二温区:=(4.0-1.5-3.0)(145-125)=-10Kw
第三温区:=(4.0+2.0-1.5-3.0)(125-85)=60Kw
第四温区:=(2.0-1.5-3.0)(85-60)=-62.5Kw
第五温区:=(2.0-3.0)(60-35)=-25Kw
5.3计算外界无热量输入时的热通量
第一温区的输入热量为0,其余各温区的输入热量为上一温区的输出热量。
第一温区: 输入热量=0Kw 输出热量=0+30=30Kw
第二温区: 输入热量=30Kw 输出热量=30+10=40Kw
第三温区: 输入热量=40Kw 输出热量=40-60=-20Kw
第四温区: 输入热量=-20Kw 输出热量=-20+62.5=42.5Kw
第五温区: 输入热量=42.5Kw 输出热量=42.5+25=-67.5Kw
5.4确定最小加热公用工程用量
在热力学上,每个温区的热通量必须大于或者等于0,明显第三温区的输出热量小于0,也即是第四温区向第三温区供热,显然是不可行的,因此需要有外来的热量向第三温区供热,也即最小加热公用工程用量为20kW。
5.5 计算最小加热公用工程时各温区的热通量
在确定最小加热公用工程为20Kw时,第一温区的输入热量为20kW,其余其余各温区的输入热量为上一温区的输出热量。
第一温区: 输入热量=20kW 输出热量=20+30=50kW
第二温区: 输入热量=50kW 输出热量=50+10=60Kw
第三温区: 输入热量=60kW 输出热量=60-60=0Kw
第四温区: 输入热量=0kW 输出热量=0+62.5=62.5Kw
第五温区: 输入热量=62.5Kw 输出热量=62.5+25=87.5Kw
由以上计算过程可知冷公用工程用量为87.5Kw,平均夹点温度为85℃,也即热夹点温度为90℃,冷夹点温度为80℃。
以上计算过程涉及到的问题表见表5-2.
表5-2 问题表
温区 | (Kw) | 无热量输入时的热通量(Kw) | 最小加热公用工程时的热通量(Kw) | ||
输入 | 输出 | 输入 | 输出 | ||
第一温区 第二温区 第三温区 第四温区 第五温区 | -30 | 0 | 30 | 20 | 50 |
-10 | 30 | 40 | 50 | 60 | |
60 | 40 | -20 | 60 | 0 | |
-62.5 | -20 | 42.5 | 0 | 62.5 | |
-25 | 42.5 | 67.5 | 62.5 | 87.5 |
6.初始换热网络设计
在完成问题表法的设计后,我们可以根据上述结果完成对初始换热网络的设计。在进行设计之前我们需要假定本设计所有物流的热容流率是不变的(实际是变化的)。初始换热网络应为最大热回收的换热网络,因此就必须没有跨过夹点的换热,所以在设计换热网络时需要将换热网络分为夹点之上和夹点之下两个系统进行设计(对于多夹点系统,需要分为更多的子系统)。本系统的热夹点温度为90℃,冷夹点温度为80℃。
对于夹点之上:
图2 夹点之上
夹点上方涉及到的物流有四条,及其所需的热量如图2所示。由图可知,夹点之上所有热物流需要300Kw的热量进行冷却,而冷物流有320Kw需要进行加热处理,多余的20Kw需要冷公用工程去冷却,与问题表法所计算量一致。
夹点上方的换热网络如图3。
图3 夹点上方的换热网络
对于夹点之下:
图4 夹点之下
夹点下方涉及到的物流有三条,及其所需的热量如图4所示。由图可知,夹点之下所有热物流需要187.5kW的热量进行冷却,而冷物流仅有100kW,其余的87.5kW需要冷公用工程去冷却,与问题表法所计算量一致。
夹点下方的换热网络如图5。
图5 夹点下方换热网络设计
该系统的换热网络如图6所示。
图6 换热网络
以上便是用问题表法进行夹点设计的手算过程,过程繁琐但结果比较可靠,通过以上设计过程可知通过冷热物流换热共回收400kW的热量,在进行工厂设计时具有很好的节能效果。随着计算机技术的发展,上述过程完全可以交给计算机完成,并且提高了计算精度和计算速度。
7.结果验证
采用问题表法的优点是我们能够更为直观的看到设计的过程,在不发生手误的情况下,结果比较可靠,而采用软件计算,我们不容易看到设计的过程,对于初学者来说不容易懂,但对于那些原理比较懂得设计人员来说,采用软件计算更为迅速,计算更为准确。基于此,本文采用Aspen Energy Analyzer软件对问题表法进行验证,物流依然采用上述物流,为了与软件的单位保持一致,对物流的相关数据进行单位转换,如表5-1。
表5-3 物流参数
物流编号和类型 | 热容流率CP/(KJ/℃*h) | 进口温度/℃ | 出口温度/℃ |
1 热物流1 | 10800 | 150 | 40 |
2 热物流2 | 5400 | 170 | 65 |
3 冷物流1 | 7200 | 30 | 120 |
4 冷物流2 | 14400 | 80 | 140 |
7.1数据提取
在Aspen Energy Analyzer软件中,数据提取包括手动输入、软件导入,我们可以通过Excel导入,也可以通过Aspen模拟文件导入,这些方法的相关教程在百度上很容易就能搜到,本文就不再详述。由于本文涉及到的物流比较少,直接手动输入,结果如图7
图7 数据提取
7.2结果验证
为了检验问题表法和软件设计的换热网络的一致性,根据问题表法的结果采用软件进行设计。根据上期的设计结果可知冷热夹点分别为90℃和80℃,冷公用工程消耗为20Kw(即72000KJ/h),热公用工程消耗为87.5Kw(即315000KJ/h),与软件设计的结果一致,如图8。
图8 软件设计结果
根据上期设计结果可知,在夹点上方,热物流1(物流1)和冷物流2(物流4)进行热交换180Kw(648000KJ/h),如果直接进行交换你会发现,设计结果错误,如图9。这似乎
图9 错误提示
与手算结果相悖,其实仔细分析便可找到原因:当交换这么多热量时,冷热物流温度发生交叉,这说明冷物流量多了,或者热物流量少了,而在热物流1的夹点上方一共就180KW的热量,这说明我们的冷物流量多了,因此我们需要将冷物流分成多股物流,根据计算结果可知,与热物流1进行换热的分物流占总物流的75%,对物流进行修改,如图10。此时物流
图10 物流修改
匹配成功,见图11。
图11 物流匹配成功
此时便完成了一个物流匹配,其他物流匹配过程与此相同,此处不再一一叙述,直接给出完整的匹配结果,如图12(此图加上了公用工程物流的匹配)。此图与问题表法的设计结果高度一致,说明软件设计的快速及可靠性。
图12 软件设计结果
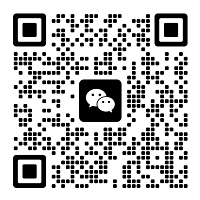
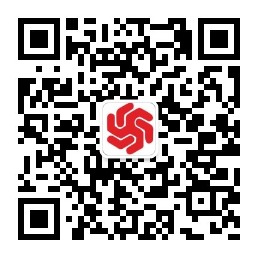
评论